高速裁线机已成为线束加工的核心设备-但裁切精度问题频发直接影响生产效率和订单交付-本文将通过-设备原理剖析-与-实操经验总结-直击裁线长短不一的痛点-提供可落地的解决方案">“上午刚调试好的机器,下午裁出的线材又出现长短误差!” 这是某电子厂生产主管张工的真实困扰。随着工业自动化需求升级,高速裁线机已成为线束加工的核心设备,但裁切精度问题频发直接影响生产效率和订单交付。本文将通过*设备原理剖析*与实操经验总结,直击裁线长短不一的痛点,提供可落地的解决方案。
一、刀片磨损或安装偏差:最易被忽视的“隐形杀手”
高速裁线机每分钟可完成数百次裁切动作,刀片磨损速度远超普通设备。若刀口出现崩刃、卷边(如图1所示),会导致线材受力不均,短边裁切时因阻力增大出现回弹,长边则因惯性拉扯产生尺寸误差。
解决方法:
每日开机前用10倍放大镜检查上下刀片咬合状态,确保刀口平行度误差≤0.02mm;
采用*碳化钨镀层刀片*替代普通合金刀片,使用寿命延长3倍;
-
定期使用塞尺测量刀片间隙,铜线/硅胶线分别控制在0.03mm/0.05mm以内。
二、送线机构异常:从“源头”切断误差链
线材输送的稳定性直接影响裁切精度。某汽车线束厂曾因送线轮胶皮老化(如图2视频片段),导致5%的线缆出现±1.5mm偏差。送线轮压力不均、伺服电机丢步、*导轮轴承卡顿*等问题,均会造成送线长度波动。
排查流程:
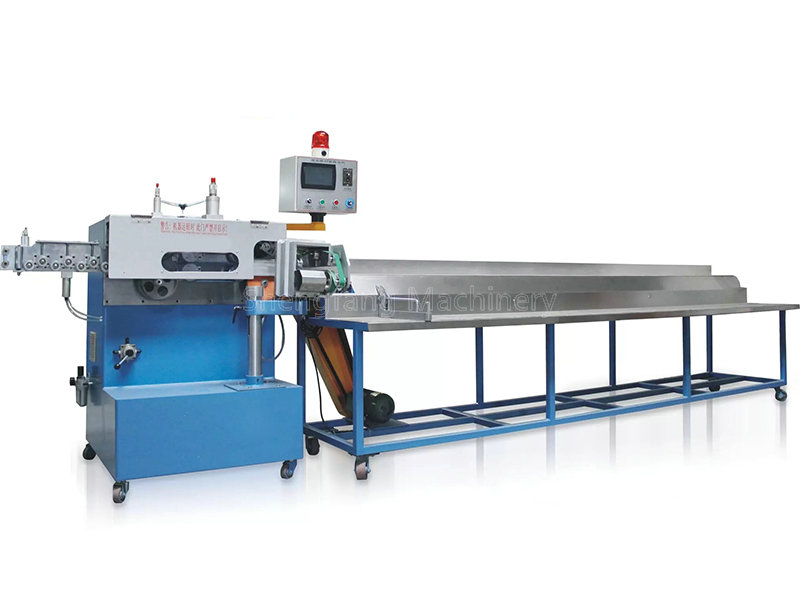
第一步:用张力计检测送线轮夹持力,标准值为2.5-3.5N(参考设备手册);
第二步:通过PLC监控界面观察伺服电机电流曲线,异常波动提示机械阻力增大;
-
第三步:用激光测距仪检测送线行程,重复定位精度需达到±0.01mm。
三、参数设置陷阱:90%的操作员都踩过这些“坑”
参数类型 |
常见错误设置 |
正确调整方案 |
裁切补偿值 |
未区分线径差异 |
铜线每增加0.1mm补偿+0.08mm |
回刀延迟时间 |
统一设为0.2秒 |
硅胶线需延长至0.35秒 |
夹线器开合时序 |
与刀片动作同步 |
提前10ms释放线材张力 |
2023年行业调研显示,38%的裁切误差源于参数配置不当。特别在处理多芯屏蔽线时,需启用动态补偿算法抵消线材回缩量。
四、材料特性引发的“连锁反应”
不同材质的线缆存在显著差异:
TPU护套线:弹性模量高,裁切后回缩率可达0.3%;
镀银铁氟龙线:硬度高,需增加20%的裁切压力;
硅胶编织线:易变形,必须配合真空吸附定位装置。
实战案例:某医疗设备厂商将PVC线材更换为TPE材质后,裁切误差从±0.1mm扩大至±0.8mm。经测试发现,预热装置温度从25℃提升至45℃后,材料延展性下降,精度恢复至±0.15mm。
五、传感器校准:用“数据思维”破解疑难杂症
光电传感器偏移0.1mm,实际裁切误差可能放大至2mm。建议每季度执行以下校准:
- 使用标准量块触发传感器,对比PLC接收信号时间差;
- 调整对射式传感器的水平倾角至≤0.5°;
- 在刀座下方加装压电式力传感器,实时监控裁切冲击力(如图3示意图)。
某新能源企业通过加装激光轮廓传感器,实现了线端平整度的在线检测,将不良品率从1.2%降至0.15%。
—
特别提示:当同时出现长短不一与切口毛刺时,极可能是主轴轴承磨损导致刀轴径向跳动超差。此时需用千分表检测主轴径向跳动量,标准值为≤0.005mm。
TAG: