“为什么刚买的自动裁线剥皮机总是裁不断线?” ——这是许多电子设备制造商和线材加工厂经常遇到的棘手问题。一台高效的自动裁线剥皮机本应提升生产效率,但频繁出现的裁切失败不仅导致材料浪费,还可能延误订单交付。本文将聚焦这一痛点,从设备设计、操作细节到维护盲区,系统性拆解裁不断线的核心原因,并提供可落地的解决方案。
一、刀片磨损或安装不当:最直接的“隐形杀手”
刀片状态是决定裁线效果的关键因素。若刀片因长期使用出现钝化、崩刃或生锈,会导致切割压力不足,线材外皮无法完全切断。例如,某线束加工厂曾因刀片未及时更换,导致每天浪费近10%的线材。
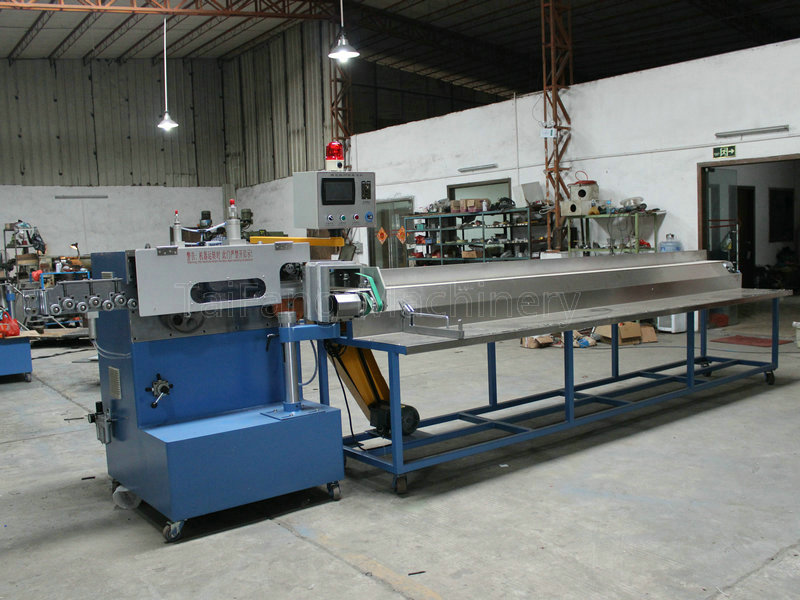
- 解决方法:
- 定期检查刀片锋利度,建议每切割5万次或发现切口毛糙时立即更换;
- 确保刀片安装角度与线材垂直,避免倾斜切割(误差需控制在±0.5°以内)。
二、气压/液压系统压力不足:动力源的“慢性病”
自动裁线剥皮机依赖稳定的气压或液压驱动刀头动作。若系统存在漏气、油路堵塞或压力阀设定值偏低(如低于0.6MPa),刀头下行力度不足,便会出现“切到一半卡住”的情况。
- 典型案例:某厂商发现裁线失败率突增,最终排查发现是气压泵滤芯堵塞导致压力下降30%。
- 优化方案:
- 每日开机前检查压力表数值是否达标;
- 每季度清洗气路/油路过滤器,防止杂质堆积。
三、线材规格与设备参数不匹配:被忽视的“兼容性陷阱”
不同材质的线缆(如硅胶线、PVC线)和线径(0.5mm²与6mm²)对裁切参数要求截然不同。若操作人员未根据线材调整刀口间距、剥皮长度或夹紧力度,设备可能因“误判”而执行错误动作。
- 参数设定黄金法则:
- 刀口间距=线径×1.2(例如2mm线径需设置2.4mm间距);
- 硅胶线需比PVC线增加15%的夹紧力,防止打滑。
四、传感器失灵:精密部件的“蝴蝶效应”
现代自动裁线机普遍采用光电传感器检测线材位置。若传感器积灰、老化或被强光干扰(如车间日光直射),可能误判线材到位情况,导致刀头提前或延迟动作。
- 某品牌维修报告显示:23%的裁切故障源于传感器信号异常。
- 预防措施:
- 每月用无水酒精清洁传感器探头;
- 为设备加装遮光罩,避免环境光干扰。
五、机械结构松动:长期磨损的“量变到质变”
长期高频使用会导致导轨磨损、螺丝松动或传动皮带拉伸。例如,某用户发现刀头水平偏移0.3mm后,裁切失败率从2%飙升至18%。
- 保养重点:
- 每周紧固关键部位螺丝(扭矩需按说明书设定);
- 每半年更换一次导轨润滑油,使用高粘度锂基脂效果更佳。
六、进阶技巧:3步快速诊断法
遇到裁不断线问题时,可按以下流程快速定位故障:
- 听声音:正常裁切时有清脆“咔嗒”声,若声音沉闷则提示压力不足;
- 看切口:切口平整度为合格,毛边/斜切口表明刀片问题;
- 测数据:用数显千分尺测量实际裁线长度,与设定值偏差>0.1mm需校准程序。
通过上述系统性分析可见,80%的裁切故障可通过规范操作和预防性维护避免。建议企业建立设备健康档案,记录每次维护数据,这不仅能减少停机损失,更能延长设备寿命30%以上。
TAG: