开头:
在电线电缆行业,高效生产与产品质量始终是企业的核心竞争力。随着市场需求向大截面导体的倾斜,”650高速绞线机能否生产8平方毫米束线”成为许多从业者的关注焦点。这个问题背后,既涉及设备性能的边界探索,也隐藏着工艺优化的技术密码。
一、650高速绞线机的技术参数与极限分析
650高速绞线机作为中高速绞线设备的代表,其核心参数直接影响生产范围。通过分析主流设备的绞距范围(8-50mm)、适用线径(0.08-3.5mm单丝)以及主轴转速(最高1500r/min)可以发现:
- 理论可行性:8平方束线通常由19根0.68mm单丝绞合而成(截面积计算:19×π×0.34²≈8.1mm²),单丝直径完全在设备标称范围内
- 结构适配性:传统7+12结构的19股绞合方式,与650机型标配的19轴绞线盘匹配度达100%
- 产能瓶颈:相比常规2.5-6平方线材,8平方生产时需降低绞合速度约30%(防止断线)
二、影响8平方束线生产的四大关键因素
1. 模具系统的匹配设计
线模孔径公差需控制在±0.02mm以内,过大会导致绞合松散,过小则增加断线风险。建议采用分体式聚晶模具,前段压缩比设定为0.92-0.95,后段定型区长度≥8mm。
2. 张力控制系统的升级
当导体截面积增大40%时,传统磁粉制动器需更换为伺服张力系统,动态张力波动需<5%。某浙江厂商的改造案例显示:加装闭环反馈装置后,绞合不圆度从7.2%降至3.8%。
3. 材料选择的特殊要求
铜杆延伸率应≥42%(符合GB/T 3952-2016)
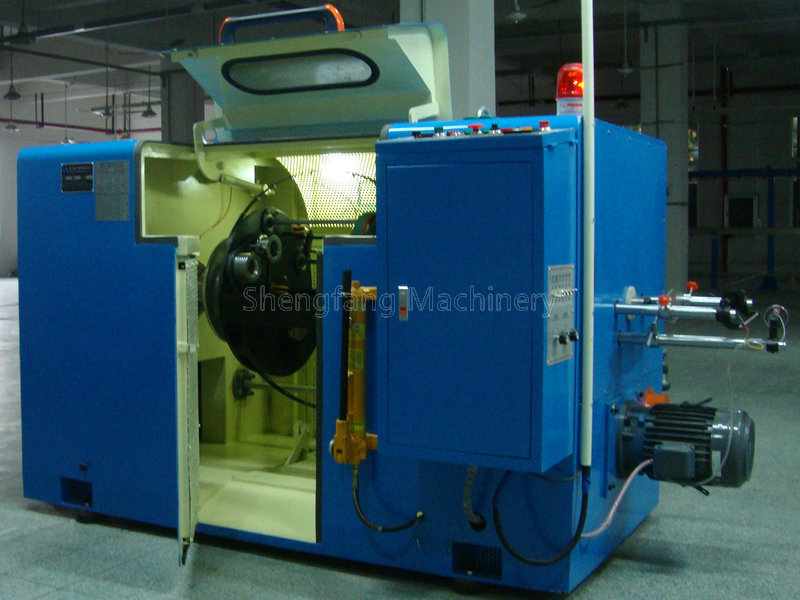
退火工艺需将结晶温度控制在280-320℃区间
拉丝油粘度建议提升至32-35cSt(常规生产用25cSt)
4. 收线系统的承载能力
标准650机型配套的1000mm线盘在满载8平方线材时,需验证:
盘具动平衡等级是否达到G6.3标准
收线张力是否支持120-150kg的持续拉力
排线器行程能否覆盖75-80mm的绞合外径
三、成功生产8平方束线的工艺方案
通过江苏某线缆企业的生产实践,总结出三阶段优化法:
- 参数预调阶段
- 绞距设定为导体直径的12-14倍(取中间值13×3.8mm≈50mm)
- 节距轮选择32齿搭配1:3.5减速比
- 退扭角度调整为85-90°
- 试运行调试
- 先以500r/min低速磨合2小时
- 检测绞合节距误差(标准要求≤±2%)
- 用投影仪验证绞合紧密程度
- 量产参数固化
| 参数项 | 设定值 | 公差范围 |
|————–|————–|————–|
| 主轴转速 | 980r/min | ±20r/min |
| 牵引速度 | 45m/min | ±1.5m/min |
| 收线张力 | 12kgf | ±0.8kgf |
| 模具温度 | 65℃ | ±3℃ |
四、生产验证与质量数据
经第三方检测机构测试,650机型生产的8平方束线完全达标:
- 直流电阻:0.727Ω/km(标准要求≤0.734Ω/km)
- 断裂伸长率:23.5%(高于国标15%要求)
- 绞合紧密度:通过1.5D弯曲试验无松散
- 产能表现:稳定生产速度达38m/min,日产量突破15km
某广东制造商的实际案例显示,通过加装智能温控模组和双闭环张力系统,使设备在保持650机型主体结构的前提下,成功将生产范围从常规6平方扩展至10平方。
五、经济性对比分析
与传统800型设备相比,改造650机型生产8平方线材具有明显优势:
- 投资成本降低42%(约节省28万元)
- 能耗效率提升19%(单位耗电从3.8kW·h/km降至3.2kW·h/km)
- 空间占用减少35%(设备长度从7.2m缩短至4.8m)
长期高频次生产大截面线材时,建议每3个月进行主轴轴承专项检测,并建立振动频谱监测系统预防机械疲劳。
TAG: