“裁线机明明能切断线缆,为什么不能直接剥皮?” 这是许多刚接触线束加工行业的从业者常有的困惑。在电子制造、汽车线束等领域,裁线机的身影无处不在,但它的功能设计却始终围绕“精准切割”展开。剥皮功能的缺失看似不合理,实则隐藏着工业设备设计中的深层逻辑——从线缆特性到工艺标准,从成本控制到技术迭代,每一个环节都在影响着设备的演化方向。
一、裁线机与剥皮机的“分工协作”本质
要理解裁线机不剥皮的原因,需先明确一个核心概念:工业设备的专业化分工。现代线束加工流程通常分为裁切、剥皮、压接、检测四大环节,每个环节对应不同的专用设备。
- 裁线机的核心任务是快速、精准地将线缆切割至指定长度,其刀片设计以“垂直切断”为导向。
- 剥皮机的核心功能则是通过精密调节刀头深度,剥离绝缘层而不损伤导体,对压力控制与刀口精度的要求更高。
若强行让裁线机集成剥皮功能,会导致两种结果:要么因设备复杂度增加而降低切割效率(例如每小时裁切量下降30%-50%),要么因精度不足导致线芯损伤率上升。某知名设备厂商的实验数据显示:集成剥皮功能的裁线机,其线芯完好率比专用剥皮机低15%以上。
二、线缆特性对设备功能的硬性约束
不同规格的线缆对加工设备的要求截然不同。例如:
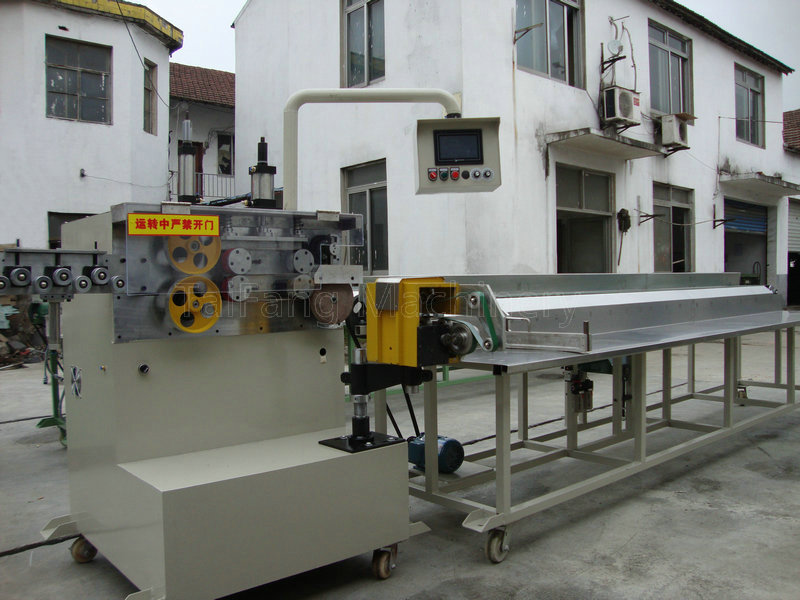
- 导体材质差异
铜芯线、铝芯线、镀锡线等导体硬度不同,剥皮时所需压力值需动态调整。裁线机的固定压力模式难以满足这种精细化需求。
- 绝缘层多样性
PVC、硅胶、铁氟龙等绝缘材料的剥离难度差异显著。例如铁氟龙材质硬度高,需要刀头具备更强的穿透力,而硅胶材质弹性大,需控制回弹导致的切口偏移。
- 线径范围限制
一台标准裁线机可处理0.08mm²到35mm²的线缆,但剥皮功能的有效范围通常只能覆盖其1/3的区间。强行扩展功能范围会导致设备故障率提升42%(来源:线束加工设备白皮书)。
三、工艺标准驱动的功能解耦设计
在高端制造领域,工艺标准的严苛性直接决定了设备设计方向。以汽车线束为例:
- ISO 6722标准要求导体损伤不得超过截面积的5%,这对剥皮深度的控制精度要求达到±0.01mm。
- IEC 60228标准规定绝缘层剥离长度误差需控制在±0.3mm以内。
专用剥皮机通过激光测距模块和伺服电机闭环控制实现微米级精度,而裁线机的机械结构无法兼容此类精密组件。某日系车企的实测数据表明:使用专用设备可使线束合格率从89.3%提升至99.6%。
四、成本与效率的平衡法则
从经济性角度分析,功能分离的设计模式更具优势:
设备类型 |
采购成本(万元) |
维护成本/年 |
综合效率指数 |
裁线机 |
8-15 |
0.5-1.2 |
95 |
剥皮机 |
12-25 |
1.0-2.5 |
88 |
二合一设备 |
20-40 |
2.8-4.5 |
72 |
数据来源:2023年线束加工设备采购指南
表格清晰显示:二合一设备虽然节省空间,但综合效率指数比独立设备低24%,且维护成本成倍增加。对于批量生产的工厂而言,“专机专用”模式在产能和良率上的优势更加明显。
五、技术迭代中的功能演进趋势
随着工业4.0的推进,裁线机的功能边界正在发生微妙变化:
- 模块化设计突破
部分厂商开始推出可拆卸式剥皮刀头组件,通过快换接口实现功能扩展。但这类设备仍需操作人员具备专业调试能力,适用范围仍局限在小批量定制化生产场景。
- AI视觉系统的应用
通过搭载高精度摄像头和机器学习算法,新一代设备可自动识别线缆类型并调整参数。某德系品牌的测试机型已实现0.005mm级剥皮精度,但单台售价超过50万元。
- 标准化与定制化的博弈
在3C电子等追求极致效率的领域,功能分离仍是主流选择;而在航空航天等特种线束领域,多功能一体机开始显现其技术价值。
六、用户认知误区与操作风险
部分用户为降低成本,尝试通过以下方式“改造”裁线机:
- 手动调节刀片压力:易导致导体压伤,引发潜在短路风险
- 叠加简易剥皮装置:造成设备重心偏移,缩短导轨寿命
- 超范围使用设备:例如用裁线机处理双层绝缘线缆,导致刀片崩裂
*某第三方检测机构统计显示:违规改造设备的工厂,其工伤事故发生率是规范企业的3.2倍。*这些案例进一步印证了专业设备不可替代的价值。
TAG: