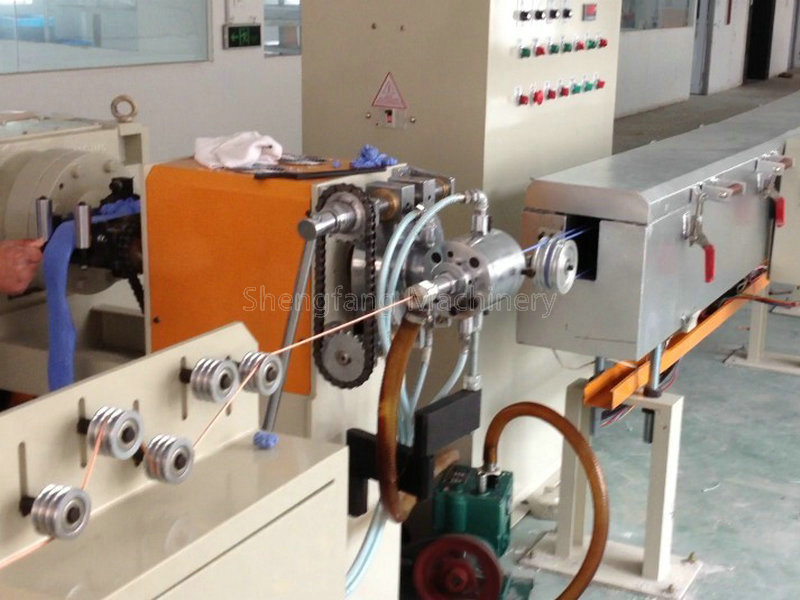
在工业生产中,押出机作为一种常见的成型设备,广泛应用于塑料制品的生产过程中。然而,在实际使用过程中,押出机出现的线径不稳定问题时常困扰着操作人员和技术人员。本文将针对这一问题进行分析,并提出相应的解决措施。
一、押出机线径不稳定的表现
押出机线径不稳定通常表现为制品直径大小不一,无法达到预设的标准尺寸。这种不稳定可能时有时无,或者呈现一定的周期性。线径的波动不仅影响产品的质量,还可能造成原料的浪费,增加生产成本。
二、造成线径不稳定的原因分析
- 温度控制不当:押出机的温度直接影响到塑料的流动性和粘度,如果温度控制不准确或波动较大,会导致塑料熔体流动性不稳定,进而影响线径的稳定性。
- 牵引速度不匹配:牵引速度与押出速度不协调也是导致线径不稳定的常见原因。如果牵引速度过快或过慢,都会使得制品的线径出现偏差。
- 模具磨损:长时间使用后,押出机的模具可能会出现磨损或堵塞,这会影响塑料的流动均匀性,从而导致线径不稳定。
- 原料质量波动:原料的颗粒大小、密度、含水量等物理性质的波动,也会影响押出过程中塑料的流动性,进而影响线径的稳定性。
- 机械故障:押出机的螺杆、传动系统等关键部件如果出现故障,也会导致线径不稳定。
三、应对措施
- 优化温度控制系统:确保押出机的温度控制系统精确可靠,定期检查和维护加热元件,保证温度的稳定性。
- 调整牵引速度:根据实际生产情况,调整牵引速度,使之与押出速度相匹配,确保线径的一致性。
- 定期维护模具:定期对模具进行检查和维护,及时清理堵塞物,必要时更换磨损部件,保证塑料流动的均匀性。
- 稳定原料质量:尽量使用质量稳定的原料,对于原料的物理性质进行严格控制,减少因原料波动引起的线径不稳定。
- 定期检查机械部件:对押出机的关键机械部件如螺杆、传动系统等进行定期检查和维护,及时发现并解决潜在故障。
押出机线径不稳定是一个复杂的问题,需要从多方面进行综合考虑和解决。通过上述措施的实施,可以有效提高线径的稳定性,保证产品质量,降低生产成本。