电线电缆生产线上,两道相似的工序设备常让从业者产生混淆——束丝机与绞线机究竟有何不同? 在导体加工领域,这两种设备虽同属线材成型机械,却在工艺原理、结构设计和应用场景上存在本质差异。理解这些区别不仅能帮助企业精准选型,更能优化线缆产品的机械性能和导电特性。
一、结构原理的本质分野
束丝机的核心功能在于实现多根单丝的同心绞合。其通过精密张力控制系统,将6-60根直径0.08-2.6mm的铜、铝单线按同心圆分层排列,每层绞向相反。典型设备采用双节距绞合技术,保证绞合节距稳定在80-120倍线径范围,这种结构使导体截面积最大化,特别适用于需要高载流量的电力电缆制造。
绞线机则专攻螺旋绞合工艺,其核心在于分线盘的动态补偿设计。设备通过行星轮系驱动线盘公转与自转,实现7-37根导体的螺旋缠绕。独特的预扭装置能消除导体残余应力,绞合节距通常控制在12-20倍线径,这种紧密结构赋予线材优异的柔韧性和抗弯曲疲劳特性,在移动设备用线缆领域具有不可替代性。
二、加工对象的显著差异
从材料适配性来看,束丝机主要处理退火软态导体。以35kV中压电缆为例,要求导体延伸率≥25%,束丝工艺能完美保持单丝塑性变形能力。而绞线机更擅长加工半硬态导体,如通信电缆用磷青铜线,其抗拉强度需达到450-750MPa,螺旋绞合产生的预应力可提升线材整体强度。
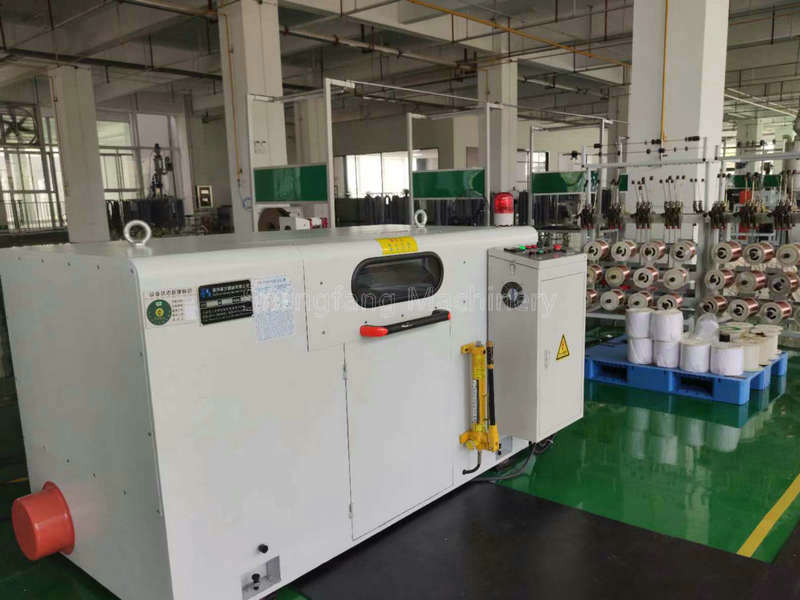
在导体规格方面,束丝机最大加工截面可达2500mm²,满足特高压输电需求;绞线机则精于微细线加工,0.016mm超细合金线的绞合精度可达±0.003mm,这对5G通信线缆的趋肤效应控制至关重要。某知名线缆企业的测试数据显示:相同截面积下,绞线工艺使高频信号传输损耗降低18%-22%。
三、工艺参数的对比分析
*速度参数*呈现明显分野:束丝机最高转速通常不超过1500rpm,重点保证绞合同心度;而高速绞线机可达4500rpm,配合恒张力收线系统,生产效率提升3-5倍。但需注意,当线径超过1.2mm时,绞线机的优势区间会急剧收窄。
*精度控制*方面,现代束丝机配置激光测径仪+CCD视觉系统,直径公差控制在±0.5%;绞线机则依赖多轴伺服联动,节距波动率≤1.2%。某德系设备厂商的实测数据表明:在0.5mm线径加工中,绞线机的椭圆度比束丝工艺降低40%。
四、应用场景的精准划分
电力传输领域是束丝机的主战场。500kV超高压电缆要求导体圆整度>98%,束丝工艺形成的致密结构能将交流电阻降低15%-20%。反观绞线机在柔性应用场景更具优势:机器人关节线缆经过36次绞合后,弯曲寿命从5万次提升至50万次,这是传统束丝工艺无法实现的。
新兴领域的需求差异更明显:新能源汽车高压线束要求导体耐温200℃+,束丝机的分层绝缘技术可集成耐高温涂层;而智能穿戴设备的0.1mm直径导线,必须通过绞线工艺实现5%以下的伸长率,确保万次弯折不断芯。
五、设备配置的关键区别
从传动系统看,束丝机多采用齿轮变速箱+电磁离合器,保证低速大扭矩输出;绞线机则标配伺服电机+谐波减速器,实现0.1°级别的转角精度。某日系设备厂商的对比试验显示:在0.08mm线径加工中,伺服系统使断线率从1.2%降至0.03%。
辅助装置配置差异更大:束丝机必须配备在线退火装置,即时消除加工硬化;绞线机则集成涡流检测仪,实时监控导体缺陷。值得关注的是,智能化升级趋势下,新一代设备开始融合两种工艺优势——某国产创新机型通过模块化设计,实现束绞工艺的智能切换,转换时间缩短至15分钟。
线缆工程师的选型决策,本质上是对产品性能与成本效益的平衡。当需要*大截面、高载流*特性时,束丝机是不二之选;而追求*高柔性、精密传输*的应用场景,绞线机展现独特优势。随着复合导体材料的普及,两种设备的工艺边界正在模糊,但对核心差异的透彻理解,始终是做出正确技术决策的前提。
TAG: