在电缆制造、金属加工等行业中,绕包机是高频使用的核心设备之一。然而,近年来因操作不当引发的安全事故屡见不鲜——某工厂因未规范操作绕包机导致机械臂失控,造成人员重伤;另一企业因忽视设备检查引发火灾,直接损失超百万。这些案例警示我们:绕包机安全操作规程不仅是生产流程的“说明书”,更是保障人员与设备安全的“生命线”。本文将系统梳理绕包机的操作标准与核心要求,为从业者提供可落地的安全指南。
一、操作前准备:从环境到设备的全方位检查
安全操作的第一步始于作业前的充分准备。根据《GB/T 3787-2017 金属加工机械安全规范》,绕包机开机前需完成以下关键步骤:
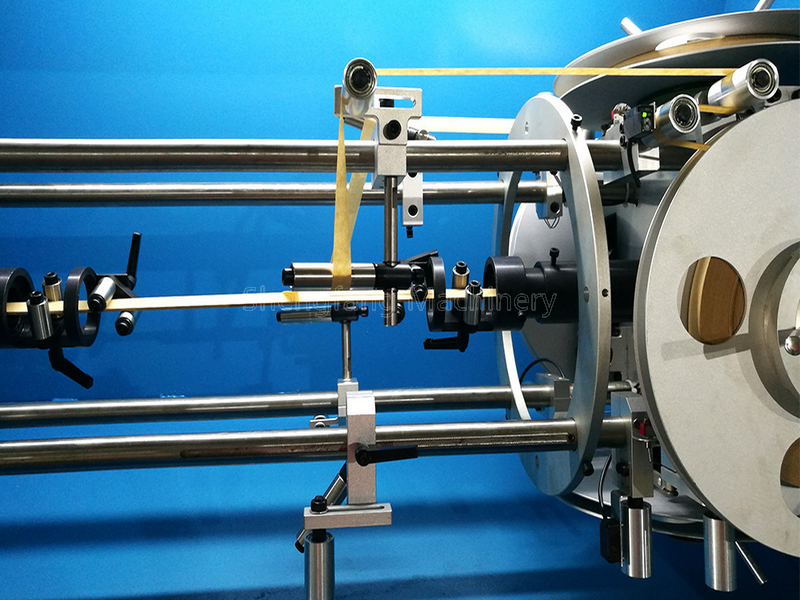
- 环境安全检查
- 确保工作区域无杂物堆积,地面干燥防滑,照明亮度≥300勒克斯
- 检查设备周边1米内无易燃易爆物品,消防器材处于有效期内
- 设备状态确认
- 重点检查传动部件(如齿轮、皮带)的磨损情况,发现裂纹或变形需立即更换
- 验证急停按钮、防护罩联锁装置的功能有效性,测试响应时间≤0.5秒
- 人员防护装备
- 操作人员必须穿戴防切割手套、护目镜及紧身工装,长发者需佩戴防护帽
- 针对噪音超85dB的环境,需配备降噪耳塞或耳罩
二、操作中规范:流程管控与风险规避
运行阶段的规范化操作直接影响事故发生率。结合ISO 12100机械安全标准,需重点关注以下环节:
- 参数设置原则
- 根据材料特性(如铜带厚度、绝缘层材质)设定绕包张力,通常控制在20-50N/mm²区间
- 转速调整需遵循“阶梯递增”原则,首次启动时应以额定速度的30%试运行
- 实时监控要点
- 每小时记录一次轴承温度,异常升温(超过环境温度+30℃)需立即停机
- 观察绕包层平整度,偏移量超过±1.5mm时必须中断作业
- 异常情况处置
- 发生材料卡顿时,必须切断电源后处理,严禁带电状态下手动调整
- 遇电气故障时,仅允许持证电工进行维修,普通操作人员不得拆卸控制柜
三、应急处理机制:构建双重防护体系
完善的事故预案能将损失降至最低。参考《AQ 7002-2018 机械安全应急预案编制导则》,应建立三级响应机制:
- 初级响应
- 设备冒烟或异响时,操作员需在10秒内按下急停按钮并疏散周边人员
- 使用干粉灭火器扑救初期火情,禁止用水处理电气类火灾
- 中级处置
- 设立半径5米的警戒区,由安全员评估现场风险等级
- 对受伤人员实施“止血-固定-转移”三步急救法,避免二次伤害
- 后期追溯
- 保留设备黑匣子数据,72小时内完成事故分析报告
- 每季度组织模拟演练,重点考核应急响应时效性与处置规范性
四、维护保养标准:延长设备寿命的关键
预防性维护可降低60%以上的突发故障。依据设备厂商提供的技术手册,需执行分级保养制度:
保养级别 |
周期 |
核心内容 |
日常保养 |
每班次 |
清理缠绕废料、润滑导轨、检查接地电阻 |
月度保养 |
30天 |
校准张力传感器、更换过滤网 |
年度大修 |
12个月 |
解体检查减速机、更新PLC控制程序 |
特别注意:润滑剂必须选用设备指定型号,混合使用不同品牌油脂会导致密封件腐蚀。保养记录需保存三年以上,作为设备状态评估的重要依据。
五、人员培训与考核体系
持证上岗是安全操作的法律底线。根据《特种作业人员安全技术培训考核管理规定》,绕包机操作员需满足:
- 完成72学时专业培训,通过理论+实操双项考核
- 每两年参加8学时复训,学习最新版安全标准
- 企业应建立“师徒制”培养机制,新员工需在导师监护下操作满200小时
通过构建“设备检查-规范操作-应急响应-维护保障-人才培育”的全链条管理体系,方能真正实现绕包机作业的本质安全。
TAG: